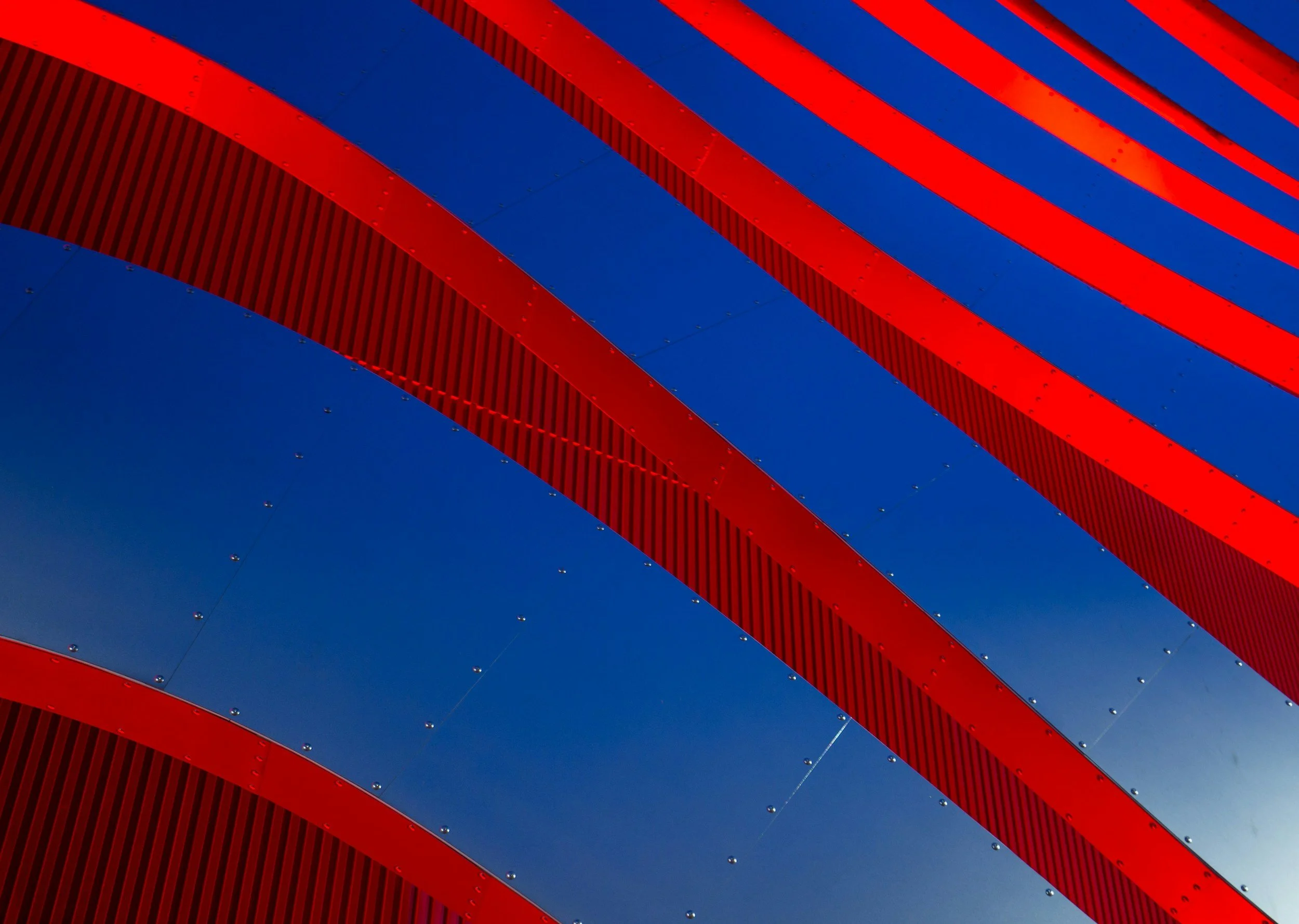
NEAL FEAY // Engineer Intern Summer 2024
Gary Lang Sample Piece // Los Angeles
The Project
This project involved creating a sample for a Gary Lang art piece, consisting of 29 intricately machined aluminum strips. Each strip was grouped into one of four finish categories: bead-blasted, polished, 180 red-grey, and 180 red. After applying these finishes, the pieces were anodized in a variety of vibrant shades and colors to achieve a dynamic visual effect. Finally, the components were assembled onto a backplate to complete the piece, showcasing a cohesive and striking design that aligned with the artist's vision.
My Role
I designed 3D models for CNC manufacturing and actively contributed to every stage of the process, including machining, finishing, anodizing, and final assembly. I oversaw the precision manufacturing of each component, ensuring that the intricate details and finishes met the required standards. My role required both technical expertise and creative input, as I worked closely to ensure the final product not only fulfilled the artist's vision but also adhered to the highest standards of craftsmanship.
220 Art Installation // New York
1/4 of fully assebled piece
The Project
The art installation for a home in the prestigious 220 building in New York was nearly 15-feet-tall consisting of 234 uniquely dimensioned panels. Each panel featured unique, ocean-inspired projected patterns, requiring two distinct and complex CNC milling operations. The machining process was highly time-intensive and required extremely high tolerances, taking approximately three hours per panel to achieve the desired precision. Beyond machining, the finishing and anodizing stages required exceptional accuracy to ensure a consistent appearance across all panels, resulting in a visually cohesive and striking final piece.
My Role
I project managed the manufacturing and test assembly of this piece, overseeing every stage of production from CAD modeling to final assembly. A key aspect of my role was dedicating significant time to learning and mastering CNC milling operations, which improved panel production efficiency and allowed me to ensure that each panel met the project's exact specifications. I meticulously tracked each of the 234 panels individually, verifying that they successfully progressed through each phase—modeling, programming, machining, finishing, and assembly—and were checked off for perfection at every stage. Additionally, I coordinated across teams, maintained stringent quality standards, and ensured smooth transitions between processes, delivering the project to completion in the most efficient and precise manner possible.
Challenges
The project faced significant challenges, particularly in successfully producing machined pieces within the high tolerances required for precise assembly. Many panels were not perfectly machined initially, requiring them to be re-machined, a process that added another three hours per piece. Additionally, scratches or damage during handling often reset the entire workflow, including machining, finishing, and anodizing, which demanded flawless execution for consistency. These setbacks taught me the importance of precision in machining and the need for strict quality control throughout every stage of production. Despite these challenges, the project was successfully completed, resulting in a cohesive and visually stunning art installation.
PGA Championship Trophy // Sponsored by Procore
Designed 3D models for the PGA Championship trophy manufactured by Neal Feay Co. Tasked with making the trophy as lightweight as possible while ensuring it remained durable and well-engineered, I maintained the same engineering and assembly plan throughout multiple design iterations. Designing for machining became a huge factor in the final design of the trophy as I learned the importance of mounting and tool paths on CNC mills. Ultimately, the trophy was divided into three parts—two halves and a base—all of which were press-fit together using pins. Each component required precision machining and tight tolerances to ensure structural integrity and a flawless assembly. This trophy was given to the first place winner at the PGA tour Procore Championship in Napa Valley, CA.
First CAD Models